Unwinding the Complexities of Lift Innovation: Troubleshooting Common Troubles Throughout Lift Versions
In the realm of lift technology, a myriad of complexities commonly lie under the surface area of what seems an uncomplicated system. From sluggish operation problems to peculiar noises originating from the machinery, troubleshooting common problems across different lift models requires an eager eye for information and a methodical strategy - repair and maintenance services. As we start this trip to unwind the intricacies that can afflict these important devices, a deeper understanding of the inner workings and potential pitfalls of lift technology is critical. Remain tuned as we browse via the labyrinth of lift breakdowns, looking for remedies to the enigmatic problems that can interfere with the smooth functioning of these important apparatuses.
Identifying Slow Operation Issues

Following, inspect the electrical links to make certain that all components are correctly attached and operating. Malfunctioning wiring or loosened connections can result in slow down procedure or total malfunction of the lift system. Furthermore, it is necessary to test the control system to determine if the concern depends on the programming or sensing units.
If the aesthetic examination and electric checks do not disclose the root cause of the slow operation, further diagnostic examinations may be essential. These might consist of stress tests for hydraulic systems, voltage examinations for electrical components, or running diagnostic software application for the control system. repair and maintenance services. By adhering to an organized strategy to troubleshooting sluggish procedure problems, you can efficiently identify and deal with the problem, making certain the lift operates securely and efficiently
Attending To Odd Noises
To successfully troubleshoot lift innovation for strange sounds, an extensive assessment of the lift elements complying with the identification of slow-moving procedure concerns is imperative. Weird noises in lifts can be a measure of underlying troubles that call for prompt interest to make certain the security and integrity of the system. Typical sources of weird noises in lifts include worn-out or misaligned wheels, damaged motor bearings, loosened or broken suspension ropes, and malfunctioning control systems. When dealing with strange noises, it is vital to carry out an organized evaluation of these components to pinpoint the precise source of the sound properly. This may include looking for any kind of visible signs of wear and tear, evaluating the functionality of motor bearings, tightening up loosened links, and lubricating relocating parts as needed.
Furthermore, it is vital to describe the lift maker's maintenance guidelines and seek aid from qualified service technicians when managing complicated lift elements or unfamiliar troubleshooting procedures. By quickly resolving strange sounds and solving underlying check my reference concerns, lift operators can make certain the optimum performance and safety and security of the lift system for guests and drivers.
Handling Faulty Control Troubles
A reliable approach for dealing with faulty control problems in lift innovation includes conducting a comprehensive evaluation of the control system's elements and functionality. When coming across problems with lift controls, it is important to very first check for any kind of loosened connections, damaged wiring, or malfunctioning sensing units. Verifying that all control displays, switches, and keypads are operating appropriately is also essential in detecting the trouble accurately.
If no visible concerns appear, professionals need to proceed to examine the control board for any type of signs of water damages, getting too hot, or deterioration, as these can commonly bring about regulate breakdowns. Additionally, resetting the control system or upgrading the software might assist resolve particular glitches or pests creating the problem.
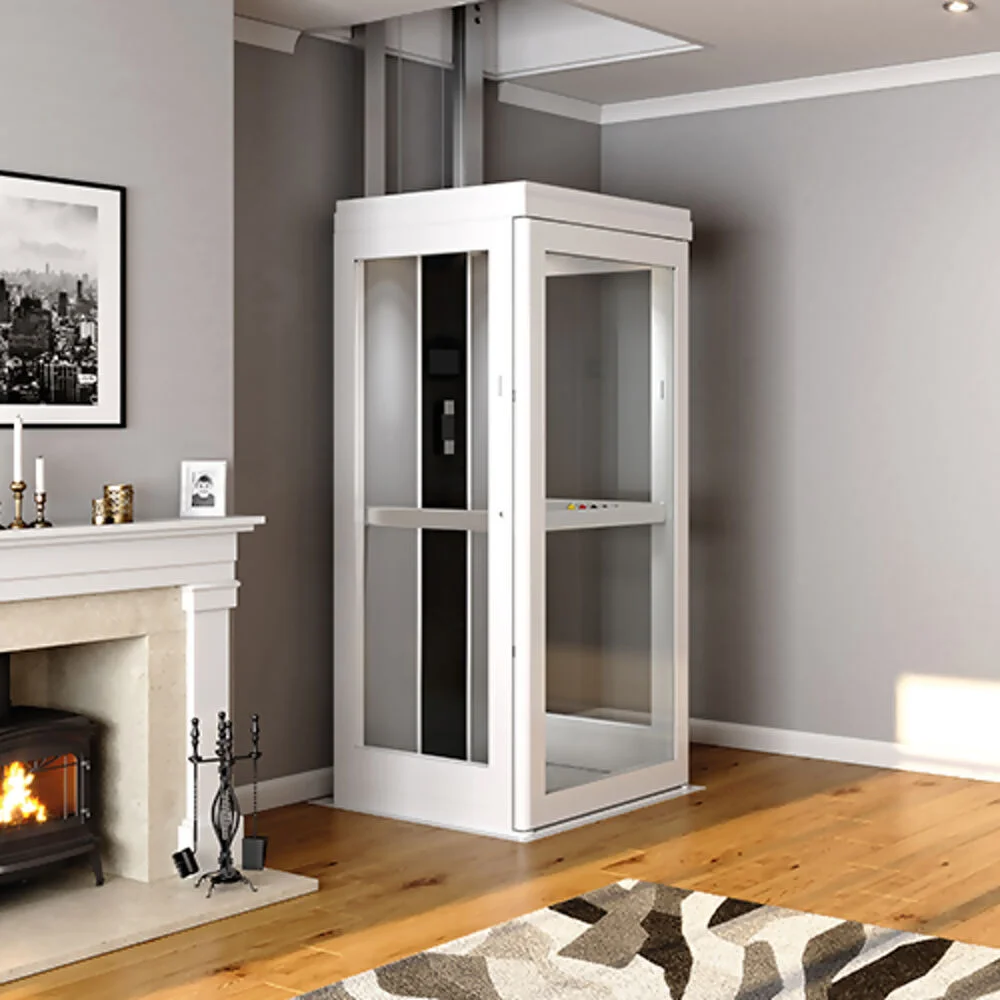
Tackling Hydraulic System Malfunctions
The performance of hydraulic systems in lifts depends greatly on the correct functioning of different components within the system. When hydraulic systems malfunction in lifts, it can lead to functional interruptions and safety problems.
Another regular hydraulic system malfunction is a loss of stress, which can arise from air going into the system, fluid contamination, or pump inadequacies. Specialists can resolve this by hemorrhaging the system to eliminate air, replacing polluted fluid, or servicing the see this pump as needed. Additionally, irregularities in hydraulic fluid levels or unusual sounds during lift procedure may indicate underlying system breakdowns that need immediate interest to avoid additional damages. Regular upkeep and timely troubleshooting of hydraulic system issues are crucial to guaranteeing the risk-free and reliable operation of lift innovation.
Dealing With Electrical Component Failings
Attending to electric component failures in lift technology requires an organized strategy to detecting and resolving concerns to preserve functional functionality and security standards. When experiencing electric troubles in lift systems, it is crucial to initial conduct a comprehensive examination of the electrical components, including control panels, electrical wiring, sensors, and motherboard. Any indicators of damage, corrosion, loose links, or burned elements should be very carefully noted and dealt with immediately to avoid more problems.
When it comes to electrical component failings, it is important to follow supplier standards for troubleshooting and repair procedures. This might involve testing the elements using multimeters, oscilloscopes, or other diagnostic devices to pinpoint the exact resource of the breakdown. Furthermore, having a comprehensive understanding of the lift's electric schematics and circuitry representations can assist in recognizing and rectifying issues successfully.
Normal maintenance and inspection schedules can aid stop electric failings by spotting possible issues at an early stage. Proper training for lift service technicians on electrical systems and parts is also important to make Check This Out certain precise diagnosis and effective resolution of electric problems, ultimately adding to the total security and dependability of lift operations.
Verdict
Finally, troubleshooting lift innovation calls for a methodical approach to determine and attend to usual problems such as sluggish operation, odd sounds, damaged controls, hydraulic system malfunctions, and electric component failures. By understanding the complexities of lift innovation and following proper fixing steps, technicians can properly resolve concerns and ensure the risk-free and effective procedure of lifts across numerous designs.
To successfully troubleshoot lift innovation for weird noises, a detailed examination of the lift elements following the recognition of sluggish procedure concerns is necessary. Odd sounds in lifts can be a measure of underlying problems that call for prompt focus to ensure the security and integrity of the system.An effective approach for resolving malfunctioning control issues in lift modern technology entails carrying out a detailed assessment of the control system's elements and functionality.The effectiveness of hydraulic systems in lifts depends heavily on the proper performance of various parts within the system. repair and maintenance services. When experiencing electrical problems in lift systems, it is crucial to first conduct a thorough examination of the electric components, including control panels, wiring, sensors, and circuit boards